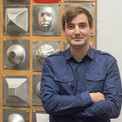
Ricardo Sousa
Bilateral Meetings
- 14.00 pm - 17.00 pm
Cork composites
Today’s society is facing the challenge to overcome issues related to pollution and material waste, increasing environmental consciousness and leading researchers to look for renewable natural resources to produce goods that keep similar properties when compared to their synthetic equivalents. The problematics of recycling synthetic foams is being taken very seriously, but full, satisfactory solutions for recycling these materials lag. Growing interest has been devoted in recent years to materials derived from renewable resources.
Among natural cellular materials, cork is the highlight. The material comes from the harvested bark of Quercus suber L tree, usually extracted every 9-12 years. Cork is a natural, renewable and recyclable material. Contrary to the majority of synthetic foams, which deform by crushing, developing permanent deformation and losing crashworthiness properties, cork is characterized by returning nearly to its original shape after deformation, being capable to withstand multi-impacts. On top of that, cork is an excellent insulator for vibration, temperature and sound.
We can offer expertise on the development of tailored cork composites for specific applications
- Outsourcing co-operation
- Technical co-operation
- Other
Incremental Forming Technology
see on http://spifa.cf
Single Point Incremental Forming is an innovative process that has the capability of producing non-axisymmetric parts. It uses simple tools, usually a cylindrical metal tool with a flat or spherical tip. It also does not require the use of dies with the shape of the piece being produced. The deformation is performed by applying pressure on the surface of the sheet, forcing it to deform gradually.
The forming tool is controlled by CNC software and the path is predefined by a toolpath processor. This results in an enhancement in the precision when compared with processes that have direct human intervention.
Advantages:
• Useable parts can be formed directly from CAD data with a minimum of specialized tooling. These can be either Rapid Prototypes or small volume production runs.
• The process does not require either positive or negative dies, hence it is dieless. However, it does need a backing plate to create a clear change of angle at the sheet surface.
• Changes in part design sizes can be easily and quickly accommodated, giving a high degree of flexibility.
• Making metal usable Rapid Prototypes is normally difficult, but easy with this process.
• The deformation mechanism based on bending-stretch and the incremental nature of the process contributes to increased formability, making it easier to deform low formability sheets.
• A conventional CNC milling machine or lathe can be used for this process.
• The size of the part is limited only by the size of the machine. Forces do not increase because the contact zone and incremental step size remain small.
• The surface finish of the part can be improved.
• The operation is quiet and relatively noise free.
Disadvantages:
• A major disadvantage is that the forming time is much longer than competitive processes, such as in deep drawing.
• As a result the process is limited to small size batch production.
• The forming of right angles cannot be done in one step, but requires a multi-step process.
• Springback occurs during the whole production phase, nowadays correction algorithms are being developed to deal with this problem.
Applications
Single Point Incremental Forming has a vast field of applications, such as aerospace, automobile, home appliances industry, marine industry and even fields such as medicine and food processing. It is a technology that is very versatile and can handle different kinds of materials, such as steel, aluminum, composite and polymeric materials. One of the major application areas of SPIF is in Rapid Prototyping because it has the capability of attaining functional parts. Another area where SPIF can have a great impact is in the medical industry, particularly in the manufacture of prostheses and braces. Using Reverse Engineering it is possible to reproduce high accurate models that mimic parts of a human body or support them.
- Outsourcing co-operation
- Technical co-operation
- Manufacturing agreement